Innovation
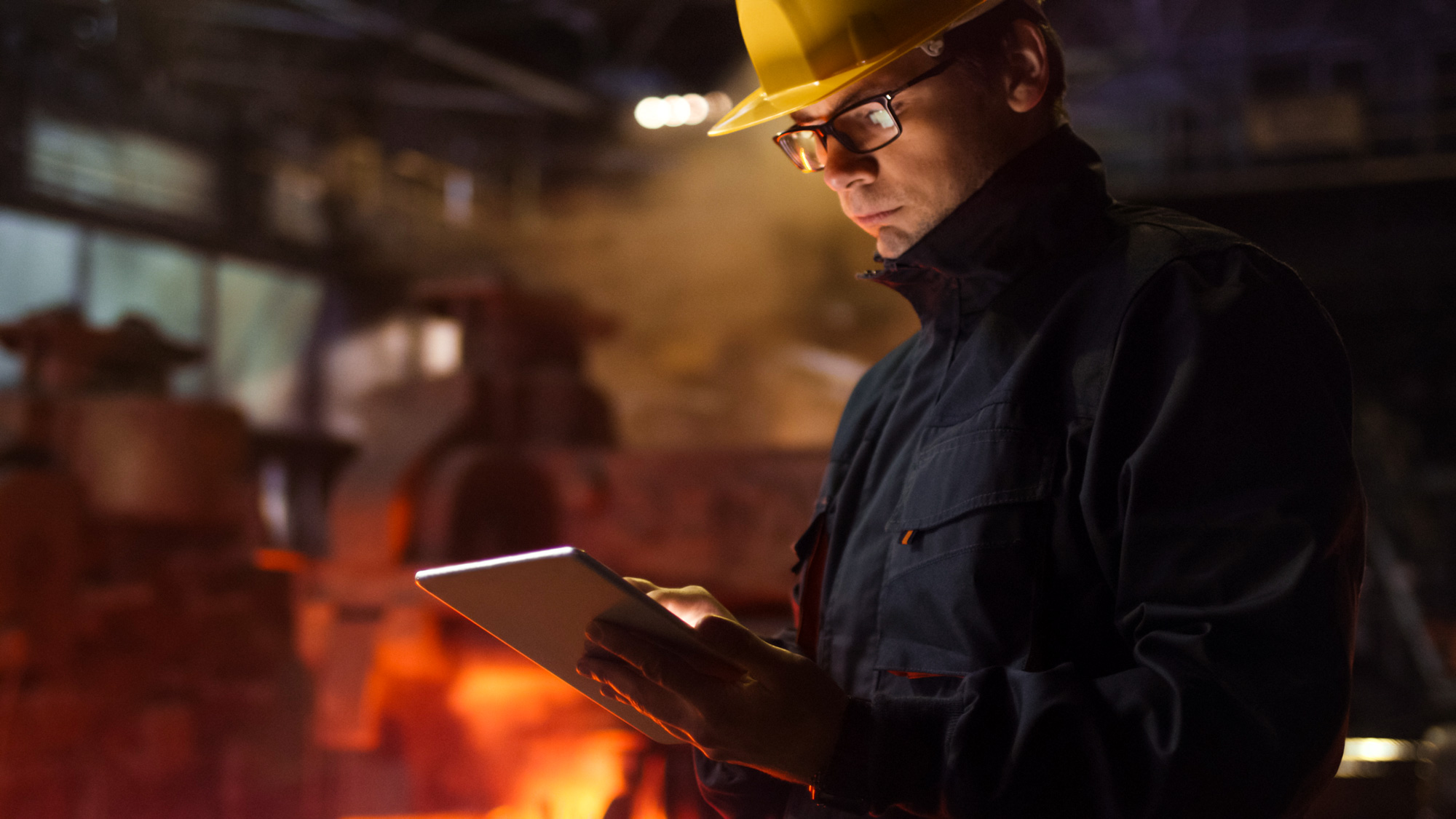
- Thanks to the Energiron Zero Reformer (ZR) process we offer a simple and most efficient plant scheme for producing higher DRI quality.
- Same process scheme for any reducing gas input.
- Use of NG/H2 in any proportion for CDA and in reversible mode at any time.
- HYTEMP System for direct HDRI feeding to EAF.
HYDROGEN: Hydrogen can be used as reducing gas for the ENERGIRON plants, without any major modification to the original process scheme. In fact, ENERGIRON plants are typically working with an H2/CO ratio in the range of 3÷5, therefore they are designed since the beginning to work with high H2 content. As a matter of fact, Hydrogen has always been the main reducing agent for this technology. Therefore, ENERGIRON is already maximizing the use of this promising energy vector, which further improves the efficiency of the reducing process. In fact, faster reducing kinetics are achieved by using H2 as primary agent, about 5 times as compared to those based on CO. Moreover, this solution allows also to minimize the CO2 emissions. In fact, the by-product of iron ore reduction by CO is CO2, whilst the by-product of reduction by H2 is water. Finally, thanks to the ENERGIRON technology, it’s now possible to produce high grade steel in an economic and sustainable way.
CO2 REMOVAL SYSTEM: The selective capture of CO2, a by-product of the reduction reactions, is an intrinsic feature of the basic process scheme. As consequence, ENERGIRON is the best-fitted technology to provide CCU (Carbon Capture and Use) and CCS (Carbon Capture and Storage) solutions applied to the steelmaking industry. Add to this the plug and play technology for Hydrogen utilization as reducing agent and the CO2 emissions per ton of steel produced can be decrease by more than 60% with respect to an integrated steel mill.