Safety & Automation
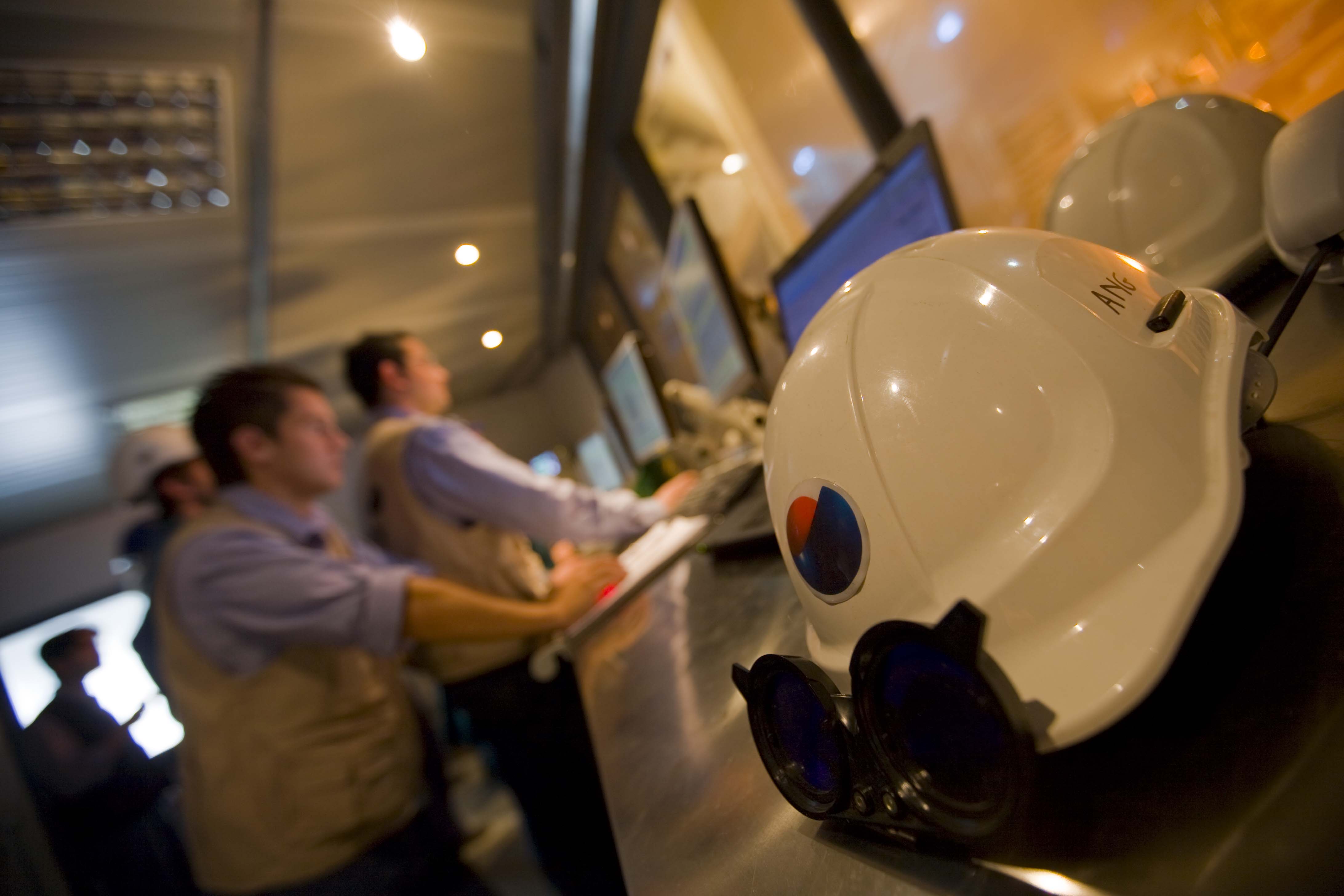
- Personnel safety is one of the design pillars of Energiron DRPs.
- Energiron DRPs have a centralized DCS that allows for safe and reliable plant operation.
Energiron plants benefit from an advanced L2 production and quality control automation system developed over decades of process know how and research.
The Energiron control system is based on an architecture consisting of a traditional Level 1 system for equipment control with a Distributed Control System, plus a new Level 2, not only for process supervision, data tracking and creation of production reports but also process optimization. A “Process Reconstruction Model” (PRM) has been developed. It uses instrumentation signals coming from the PLC and physical equations in order to provide a full description of the plant status. In this way it is possible to calculate many normally unmeasurable items such as the top gas composition and relevant red/ox ratio.
Another target of this PRM is the Product Quality Prediction; starting from the gas composition measured by the mass spectrometer, we can predict with sufficient lead time (from 6 to 10 hours before the material is discharged) the characteristics of the product, such as metallization, carbon content and DRI temperature. As a consequence the process engineers have a consistent margin in terms of time to adjust the process parameters in order to reach the desired production both in terms of quality and quantity. Further innovative Level 2 functionalities based on the Extended Kalman Filter Estimator and the Linear Quadratic Gaussian Regulator for calculation of the optimal Level 1 set points as a function of the Level 2 requested inputs will drive the future development of the advanced DR Process control.
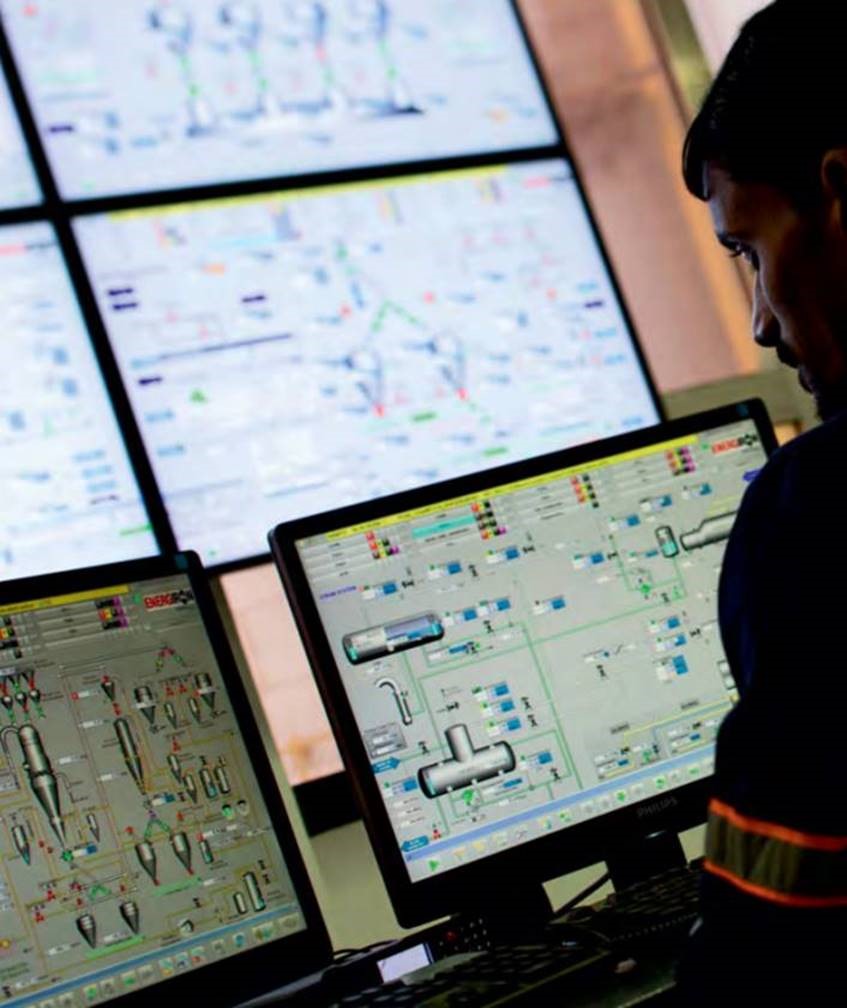