Technical data
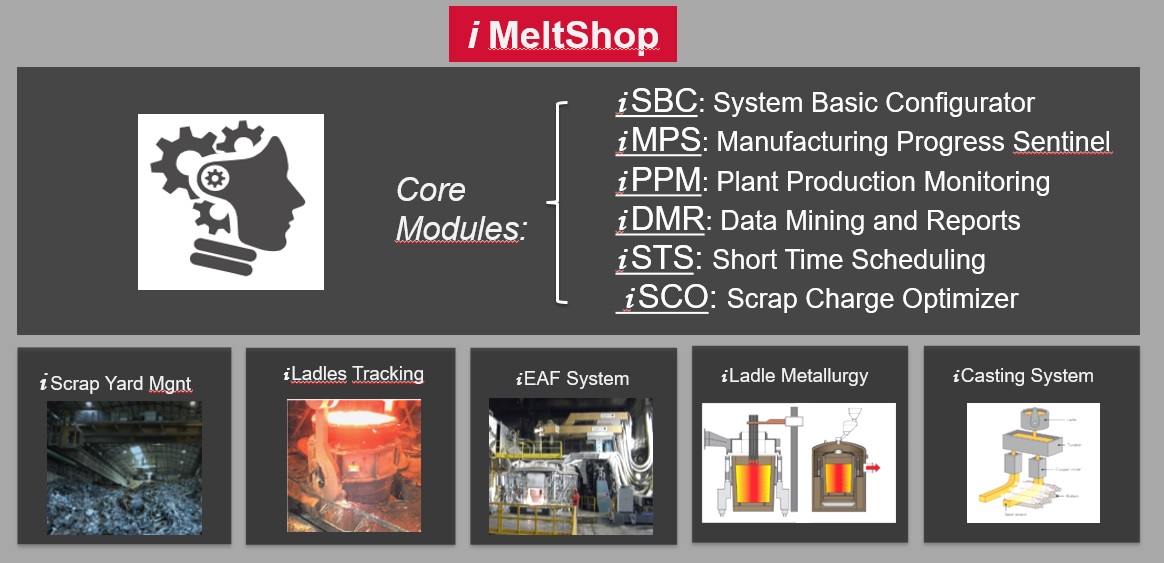
Tenova iMeltShop has been designed using a highly modular structure.
Tenova iMeltShop system consists of fundamental modules (CORE) and optional modules that add functionality and control capabilities to the system.
iMeltShop is therefore a scalable, configurable and expandable system, in order to allow the best adaptation to different production realities and possible future needs.
iSBC: SYSTEM BASIC CONFIGURATOR
This digital twin of the plant replicates all logistics and process dynamics within the plant, from the process time at the furnace, to the casting sequences, to the movement of cranes and cars. Being an offline tool, it can also be used to predict the effect on the operations of the plant upon the implementation of major changes (i.e. relocation or upgrade of equipment, the addition of a LF or of a crane etc.).
iMPS: MANUFACTURING PRODUCTION SENTINEL
This online intelligent module optimizes and coordinates the entire production line in real time. It is the core of iMeltShop. It optimizes the operative procedures and it is able to simulate the best alternative route whenever there is a problem on the standard production route. This intelligent solution is proposed in real time to the operators, taking into account the products in the pipeline (from the ERP) and the actual conditions of the equipment in the plant.
iPPM: PLANT PRODUCTION MONITORING
This module updates the schedule of production flow and performs a predictive estimation of delays using dynamic data analysis. The results are presented as time diagrams (eg Gantt chart) covering the whole process route and as “control cards”, customizable cards that show the key process parameters the customer decides to represent.
iSTS: SHORT TIME SCHEDULING
Support in defining and managing steel meltshop production programs for a period up to 72 hours. It generates the best casting sequence, taking into consideration production targets and possible constraints.
iDMR: DATA MINING & REPORTS
A flexible and fully customizable module that allows the user to create and extract any type or report from recorded data. Reports can be digital or printed. It also allows the monitoring of specific KPIs and can give automatic warnings whenever a certain parameter is out of the specified range. It is a fundamental tool for the continuous improvement of the operations and of the team.
iSCO: SCRAP CHARGE OPTIMIZER
iSCO module performs the scrap charge optimization, in compliance with the general strategy assigned, searching for the minimum value of the overall cost
index defined as the sum of the costs of:
- Cost of the composition of materials in charge, considering the only ones currently available
- Cost of transformation (electrical power, chemical power, slag former, etc.) for the materials considered.
The result of this strategy is to ensure the effective lower cost of the entire melting process.