Innovation
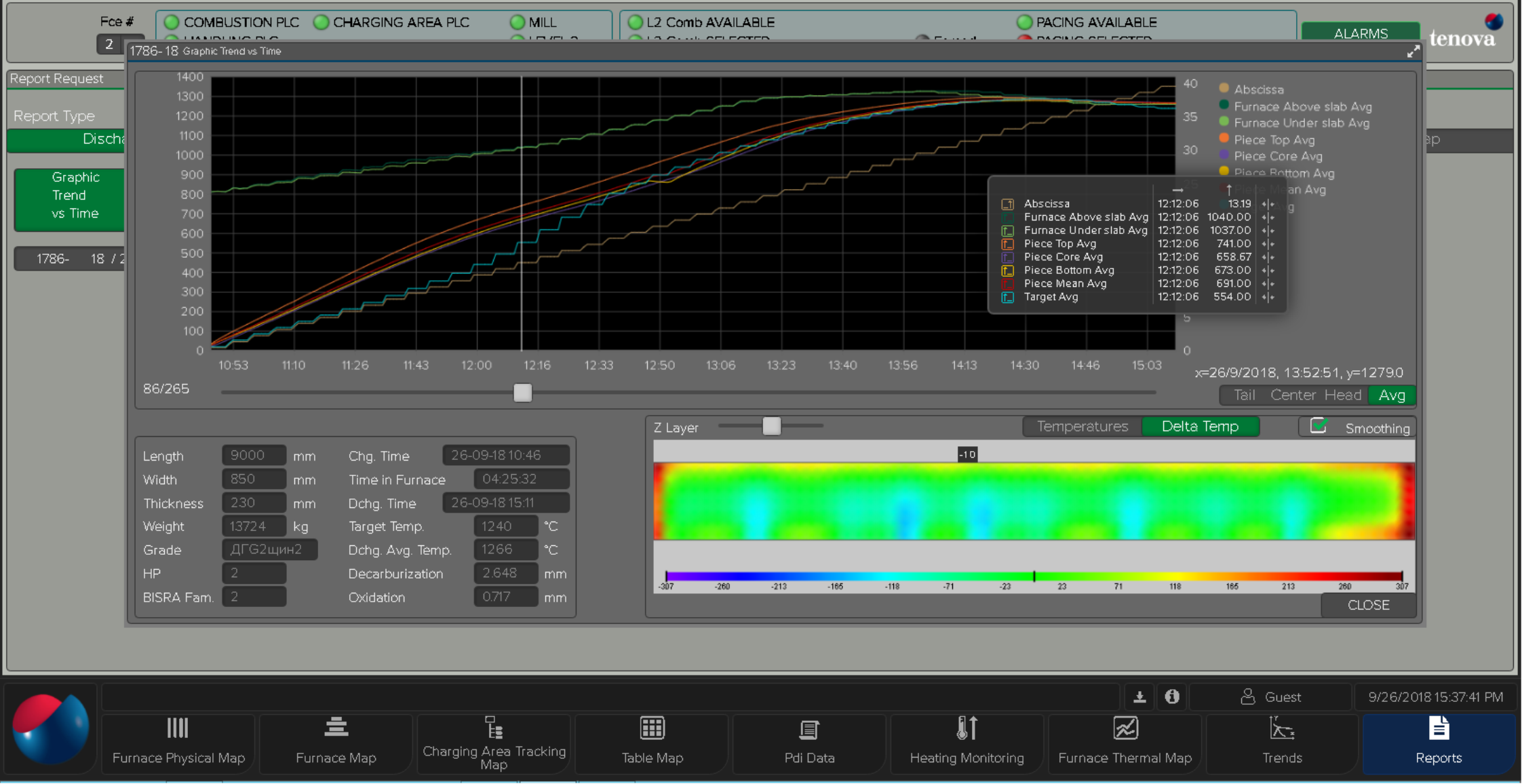
Tenova is on the forefront of the innovation: dedicated teams are involving experts for a continuous development of advanced equipment, software solutions and models.
All the equipment are designed and verified under dynamic conditions, which simulate the actual operating condition at plant.
The design on the furnaces is made by in-house software suite Tenova Caltec which includes several tools for :
- 3D heating process modeling
- Billet properties predictions
- Mechanical and handling design
- Combustion system design
The results have been validated through the years by dedicated tests and field data collection assuring the reliability of the software’s tool.
The online mathematical model Level 2 System is a powerful tool for protecting the environment and raising the gains and the final product quality, by:
- A decrease in fuel consumption by promptly adapting the combustion rate to any production rate
- A decrease in NOx and CO2 emissions
- A decrease in decarburization of the billet/slabs with a valuable effect on product quality and quantity
- A precise control of the required dropout temperature with a massive impact to the rolling mill performance
Tenova has a long tradition in leading edge combustion technology and developed an interdisciplinary design process including Computation Fluid Dynamics (CFD) modeling, industrial scale test and industrial applications.
The above mentioned workflow allows to drastically reduce the time to market for the development of new burners and combustion system.
The Italimpianti furnace department hosts a team of refractory experts which are fully committed to continuously improve the furnace lining performances and reliability by dedicated material selection, relevant engineering, test on field and the release of Tenova’s pre-casted pre-fabricated components.