Roller Hearth Furnace for Pipe & Tube
LOI Thermprocess, with its predecessors Matthias Ludwig and Nassheuer, has been building Continuous roller hearth furnace plants under protective gas atmosphere for tubes, bars, wire coils and semi-finished annealing goods for more than 60 years. Throughout the world, more than 350 LOI roller hearth furnace plants under protective gas atmosphere have been installed
Overview
Carbon Steel
Carbon and low-alloy steel is annealed at temperatures up to 1,050 °C in a process gas atmosphere. Bright annealing combined with
- stress relieving annealing
- recrystallization annealing
- normalizing
- tempering
- soft annealing
- solution annealing
- isothermal annealing
is the most important heat treatment procedure in roller hearth furnaces.
In the process gas, nitrogen is mainly used as carrier gas. Hydrogen e.g. is added to it, which reduces, among other things, the oxide layers on the material surface and thus achieves the blank annealing effect.
We apply a process technology particularly for the carbon-neutral annealing of steel that precisely regulates the proportion of carbon in the atmosphere by measuring the dew point. The so-called C-level control creates the optimal conditions for the heat treatment of the material surface. Under certain conditions, this technology is also applicable for carburizing annealing.
Depending on the process requirements or the local availability of the reaction gas – such as e.g. endogas, monogas, exogas or split ammonia – our experts optimize the process parameters with which the desired product properties are reliably achieved.
In contrast to stainless steel, the annealing good must not be cooled too quickly downstream the furnace chamber in order to ensure a uniform distribution of the structure and minimal distortion of the final products.
Individually adapted to the customer's needs, we apply various cooling concepts. Since these concepts mainly focus on efficiently using the “waste heat”, the low-temperature and high-temperature cooling sections are not only equipped with heat recovery units, but they are additionally coupled with each other. In addition, the energy from the exhaust gas of the burner device can optimally complement and round off the heat recovery. Furthermore, the energy from the burner waste gas can optimally complete and round off the heat recovery.
The different types of jet cooling are integrated at appropriate places in the segments of the radiation cooling section to implement a particularly small construction length of the entire furnace.
Up to twelve tons of heating good are treated per hour in our roller hearth furnaces for normal steel. Leading steel pipe manufacturers apply our furnace plant technology throughout the world. We design furnaces higher throughput in accordance with our customers’ requirements.
Stainless Steel
Bright annealing combined with solution annealing is the most important heat treatment procedure for stainless steel tubes in roller hearth furnaces.
The heat treatment usually takes place at temperatures of max. 1.250 °C. To achieve the bright annealing effect, an atmosphere of 100 % hydrogen is used as reaction gas during the heat treatment.
Moreover, the furnaces are suitable for
- stress relieving annealing,
- recrystallization annealing,
- normalizing, and
- soft annealing.
During the annealing of stainless steel, hydrogen mostly is the active or reactive component of the process gas. Nitrogen, in special cases argon or helium, is used for the furnace purging and forming. The selected instrumentation and used purging gases ensure a furnace operation at the highest safety level. A sophisticated safety logic guarantees safety for the personnel, machines and material at all times of operation.
Since a rapid material cooling is crucial for stainless steel, our furnaces distinguish themselves with a particularly short design of the physical separation between the heating and cooling zone. Due to jet coolers immediately downstream the furnace chamber, we achieve temperature gradients of more than 5 K/second at the latest in the range of 900 to 400 °C. Moreover, the recirculation fan speed can have an impact on the cooling gradient.
LOI’s roller hearth furnaces also suit duplex and super duplex steels that require a precisely adapted atmosphere. In our furnaces, the proper setting of the dew point avoids the individual annealing materials "sticking" together“.
In LOI’s roller hearth furnaces for stainless steel, currently up to two t/h of annealing good with a component length of max. 38 m are heat-treated in top quality. Leading manufacturers of stainless steel pipes apply our furnace plant technology throughout the world.
We design furnaces for longer products or higher throughput according to our customers’ requirements.
Nonferrous Steel
Non-ferrous metals are usually annealed at temperatures of up to 950 °C in a controlled protective gas atmosphere and in compliance with the well-proven high convection principle. The bright annealing combined with
- stress relieving annealing
- recrystallization annealing /soft annealing
- homogenising
- precipitation hardening
- is the most essential heat treatment procedure.
Non-ferrous metals are usually annealed under nitrogen as a protective gas. Due to the particularly high affinity of some materials to oxygen, vacuum locks are used in the heat treatment. A pre-purging unit including the option of automatic docking can be integrated in case of hollow products (e.g. pipes) which are often delivered as coil. This pre-purging unit floods the inside of the profiles prior to their transport into the vacuum chamber. This step ensures that the material surface in the inner tube does not react with any possibly penetrated oxygen from the ambient air during the annealing process.
Thanks to a special atmospheric circulation and the controlled atmospheric flow, we guarantee a particularly homogeneous heating-up and minor temperature tolerances in the process.
Related Solutions
Europe
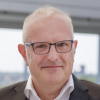
Holger Kehler
General Manager Sales Heat Treatment Flat Products, Tenova LOI Thermprocess
Modernization, Service & Spare Parts
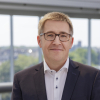
Marc Reynaert
Head of Revamp & Modernization, Tenova LOI Thermprocess