Twin-Chamber Melting & Recycling Furnace TCF®
The TCF®-process developed by Tenova LOI Thermprocess generates clean, recycled aluminium from contaminated end-of-life scrap with sticking oil, grease, lacquer, plastic or other organic contamination without the need for thermal pre-treatment or the use of salt.
Overview
All process steps for the scrap recycling until discharging the liquid metal take place in one single aggregate. The TCF® process distinguishes itself with an extremely high metal yield of the metal recovery.
The heat recovery with regenerators using ceramic elements and the integrated post-combustion of the carbonization gases resulting from the contaminants reduce the energy required for the process. The TCF® process is thus the ecologically and economically appropriate solution for the recycling of aluminium.
Since the TCF® process does not need salt addititves, the resulting dross processing is less costly.
Design
The Twin-Chamber Melting Furnace TCF® consists of heating chamber and scrap chamber accommodated in one furnace casing. Although they have a common melt bath, their atmospheres are separated from each other. While the scrap chamber operates with an almost oxygen-free atmosphere, the heating chamber with the main burners provides optimum conditions for the complete combustion of the pyrolysis gas that evaporates from the adherent organic contaminants during the scrap heating in the scrap chamber.
The liquid metal continuously circulates between both furnace chambers so that in the melt bath a uniform temperature and chemical distribution results. For this purpose, the furnace uses an electromagnetic pump or stirrer.
Wide door openings and smooth interior walls allow easy charging, cleaning and inspection of the furnace.
Operation/Handling
The scrap is placed on the dry hearth of the scrap chamber, where it is preheated, dried and pyrolysed.
In addition and unique to the TCF®, we have integrated a further process step: Thermolysis. Depending on various monitored parameters, the control system of the plant allows for adding defined quantities of oxygen to enhance the thermal pretreatment of the scap. This process step further reduces the dross generation and improves the metal yield.
By loading the next fresh scrap charge, the pretreated scrap moves onto the melting bath for melting. When using an electromagnetic pump, small pieces of scrap, chips or alloying elements such as magnesium or silicon can be easily fed into the optional charge well. Block metal can directly be fed into the heating chamber.
The molten metal is discharged from the furnace via a classic tapping or by use of a pump.
Integrated Waste Gas Treatment
The regenerative heating system specially developed for the TCF® process quenches the waste gas and preheats the combustion air, which reduces the energy consumption and protects both resources and environment.
The pyrolysis gas developed in the scrap chamber during heating the fresh scrap material is transferred to the heating chamber, where it is burnt completely. Its energy content contributes directly to heating the furnace and to reduce the energy requirement of the furnace.
The regenerator CCR fulfils several tasks at the same time: On the one hand, it extracts energy from the waste gas for preheating the combustion air. On the other hand, it quenches the waste gas leaving the furnace at a rate of 2,000 K/second. Consequently, the De-novo-synthesis is prevented.
The advantages at a glance:
- Optimum metal yield
- Less dross generation
- No external upstream pre-treatment of the scrap required
- Minimum energy requirement by using the energy content of the contaminants and by preheating the combustion air
- Recycling without using salt
- Fully automatic operation
Related Solutions
China
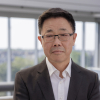
Peizhong Wang
Director of Sales Tenova LOI Thermprocess, Tenova Technologies (Tianjin)
Modernization, Service & Spare Parts
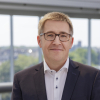
Marc Reynaert
Head of Revamp & Modernization, Tenova LOI Thermprocess