Tenova and ORI Martin’s innovative Lighthouse Acciaio 4.0 set the standard for a fully integrated supervision of the steelmaking process, harnessing the enabling technologies of Industry 4.0 to make it smarter, safer, and more sustainable. A remarkable story of the value of collaboration as a key tool for forging pathways to innovative and green manufacturing processes.
Steel is one of the most important engineering and construction materials in the world. It is a core pillar of our society, used virtually in every aspect of our lives, from the humble tin to the latest EVs and computer chips. Due to its versatility and recyclability, it has a leading role in the green energy transition.
As one of the biggest steel producers in the world, Italy (which ranks 11th according to the most recent World Steel Association report) plays a strategic role in the steel industry, and, together with the EU, enables a net-zero economy by driving green steel production. Recent funding from the Italian Ministry of Economic Development (MISE) and Regione Lombardia, allowed Tenova to partner with ORI Martin – an Italian company producing special steels for automotive and mechanical engineering – on the Lighthouse Acciaio 4.0 project tasked with making steelmaking smarter, more resilient, and more sustainable.
One of four lighthouse projects selected by the Italian Smart Factory Cluster (Cluster Fabbrica Intelligente - CFI) in 2019, Acciaio 4.0 successfully developed a Cyber-Physical Factory that, thanks to the enabling technologies of industry 4.0, produced superior quality steel from ferrous scrap, boosted plant efficiency, and reduced accidents by monitoring human presence in hazardous areas or employing robots in potentially dangerous operations.
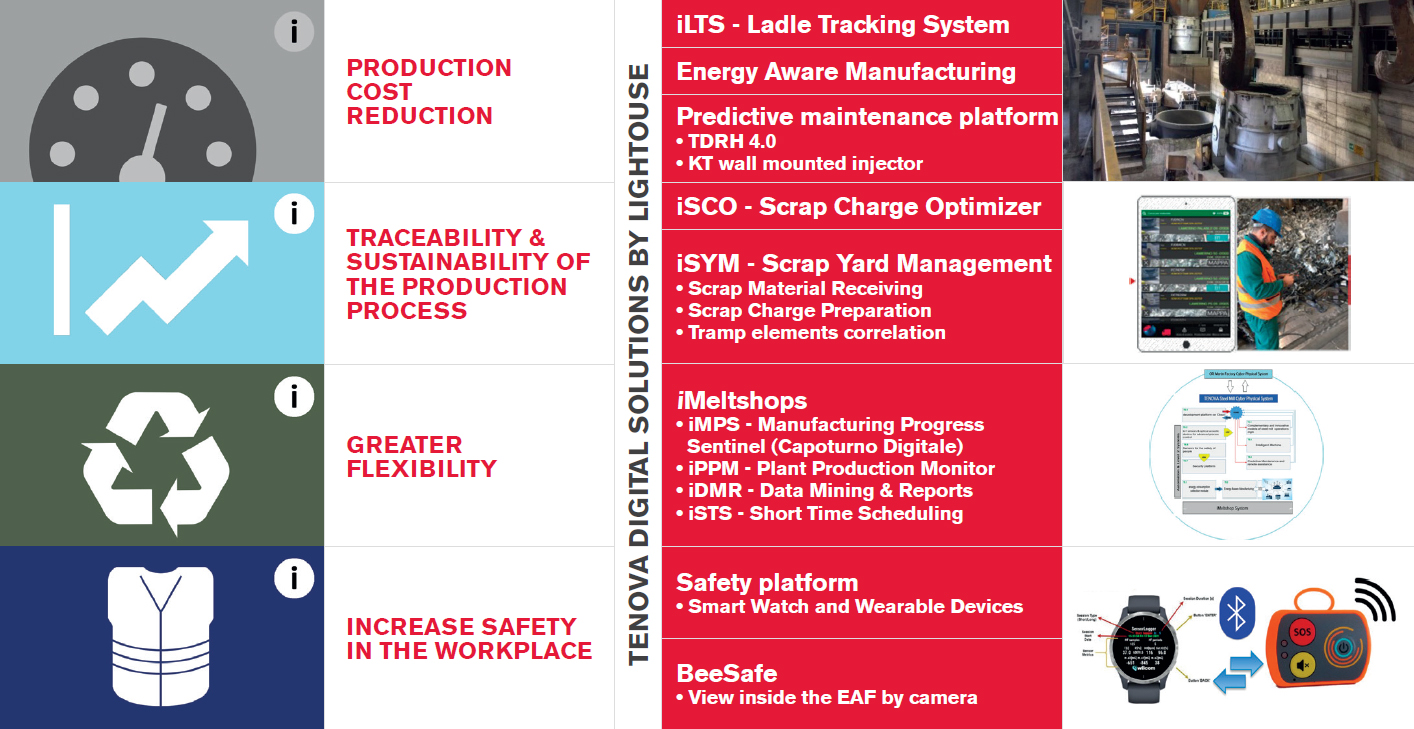
The term “cyber-physical factory” was coined to describe a plant capable of a fully integrated supervision of the production process. It was the first model of massive application of the Fourth Industrial Revolution’s most innovative technologies.
The project was divided into two phases. The first involved investing in the ORI Martin plant to acquire advanced technology and services for improving machine and device connectivity to subsystems with their own rules and intelligence. CRM, a digital customer relationship management system, was also introduced. The second phase focused on implementing innovative models of integrated process control for the plant, drawing on Industry 4.0 enabling technologies, including cloud, smart sensors (IoT), big data analysis, robotics, and new sensors.
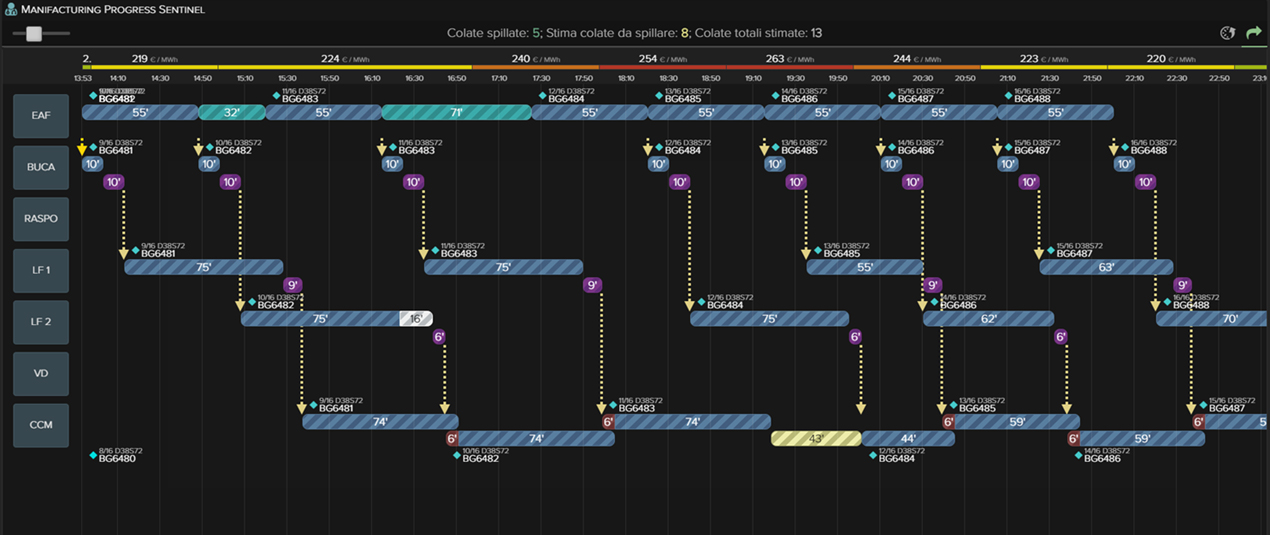
The Lighthouse Acciaio 4.0 concluded successfully in May 2023, with all modules installed at ORI Martin. Our digital solutions have enabled the ORI Martin steel mill to reduce costs, enhance liquid steel quality, and improve safety in various aspects, including scrap supplier selection, optimizing EAF charge, reducing electrode breakage, monitoring maintenance activities, and energy-efficient production planning.
Artificial Intelligence and Machine Learning were used extensively in the scrap management application to:
- Automatically classify incoming scrap material on trucks, comparing it with material in the relevant purchase order, and issuing warnings for mismatches.
- Identify bulky scrap on the Consteel® charging conveyor, to prevent damaging electrodes when material enters the furnace.
- Classify the scrap on the Consteel® conveyor for more precise control over the furnace charge.
- Determine tramp element levels for each combination of scrap type and supplier, aiding supplier evaluation and controlling liquid steel composition.
Additionally, data gathered from the plant and from new sensors and cameras enabled several features, including:
- Accurately estimating grabbed scrap weight while the cranes are in motion, using advanced algorithms developed by ORI Martin & CSMT.
- Making real-time predictions of steel composition changes concerning the mix of scrap moving toward the conveyor, with the possibility of preventing potential drifts and suggesting scrap variations during the process.
The project enabled an environmental impact assessment based on Life Cycle Analysis (LCA) in collaboration with CNR-STIIMA, considering a comprehensive range of environmental impact categories as defined by ISO 14040/44.
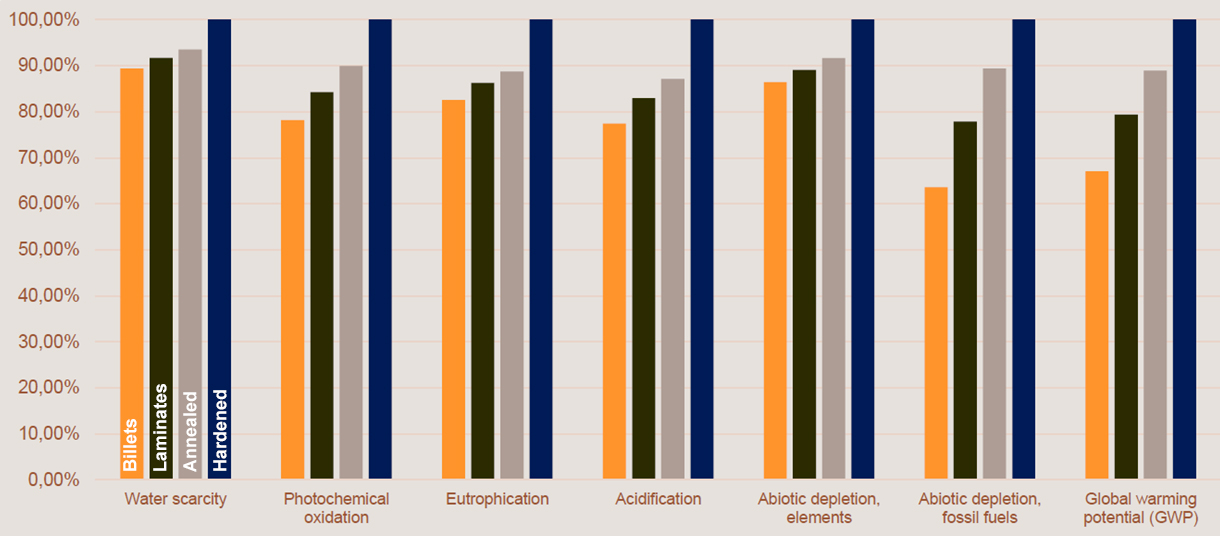
Related technologies
Want to know more?
Get in touch with our experts on the subject