The EU-funded project OnlyPlastic demonstrated the crucial role circular economy can play in the decarbonization of the steel sector. The project successfully reduced the emissions of Electric Arc Furnaces by replacing fossil raw materials with a new product obtained from waste plastic residues. Tenova developed an innovative injection technology that significantly lowers CO2 emissions as well as reducing landfilling, underscoring its commitment to the circular economy and a sustainable future.
It is a well-established fact that the decarbonization of production processes is one of the main pathways to transform the steel industry into a climate-neutral sector by 2050. Globally, a welcoming number of new technologies and processes have been developed, based on the massive use of renewable electricity and green hydrogen. They play a critical role in this transformation, however, decarbonizing a hard-to-abate sector is no small task – sectors like ours require very high investments to address transformation. Collaboration, then, becomes essential and drives the creation of some of the most innovative solutions that advance our sector’s pathway to net zero. This is the case with OnlyPlastic, an EU project funded by the Research Fund for Coal and Steel that successfully reduced emissions of Electric Arc Furnaces (EAFs) by replacing fossil carbon with a Secondary Reducing Agent (SRA) obtained from plastic residues, injected by Tenova’s novel injection technology.
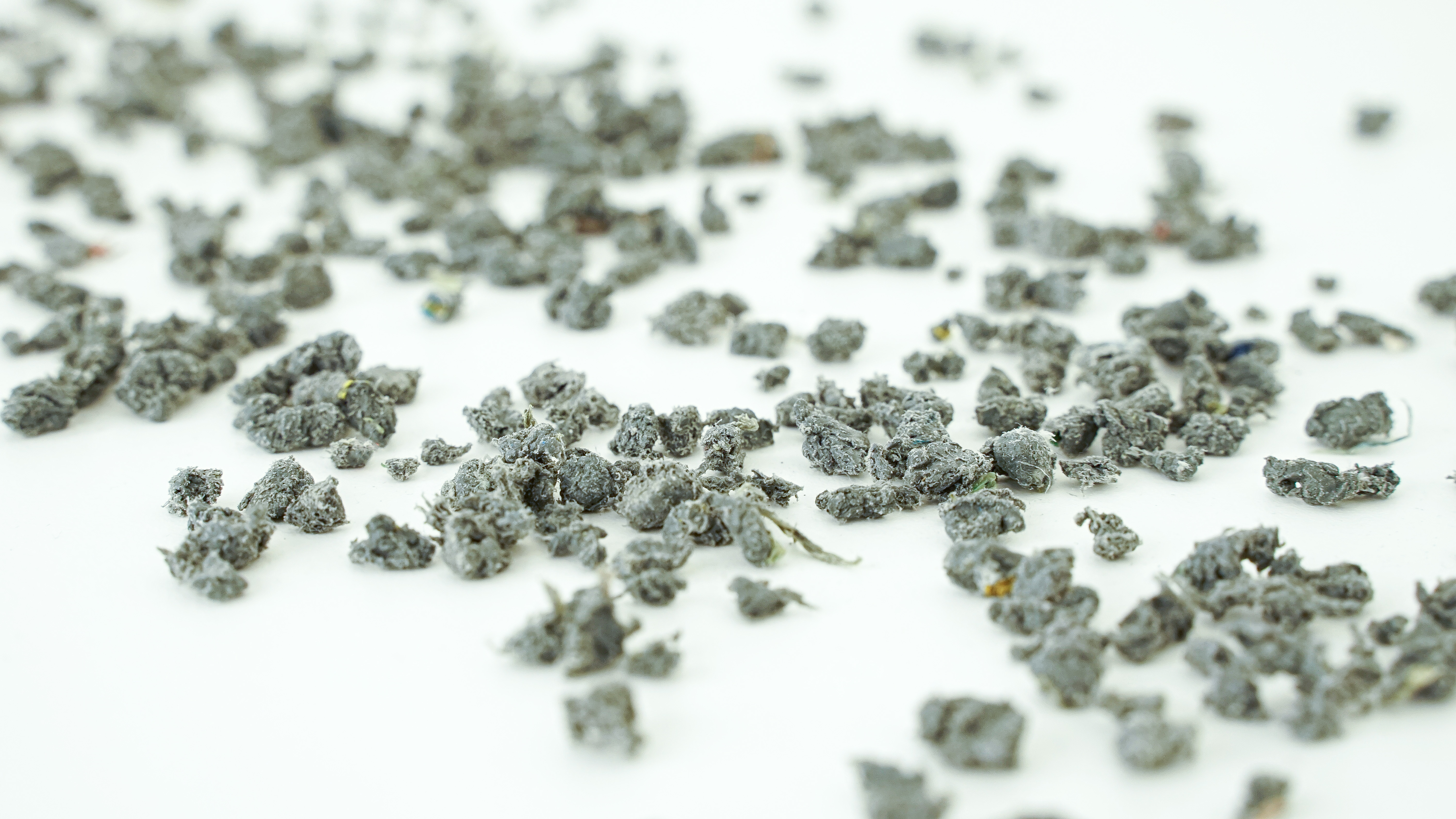
Steelmaking based on scrap melting in EAFs is one of the most promising solutions to lower emissions as opposed to iron ore melting with Blast Furnaces (BFs). There is always room for improvement, especially when it comes to reducing emissions from fossil raw materials, and OnlyPlastic is an excellent example of circular economy in action. It plays a key role as it allows the replacement of coal with alternative materials derived from other production processes – in this instance, from the residues of waste plastic treatment plants, therefore also reducing landfilling.
The substitution of coal with other carbon-rich materials in iron and steel production is not new: Voestalpine Stahl BF (Linz, Austria) was the first steel company to do so, partially substituting the coal in the tuyeres with a raw material derived from the production residues of household waste plastic treatment plants. OnlyPlastic aimed to transfer this best practice to EAF-based steel production as well, promoting a symbiotic approach between different industrial sectors in agreement with the “Circular Economy” goals promoted by the EU.
OnlyPlastic, which lasted from 2019 to 2023, was a partnership coordinated by RINA, the multinational engineering consultancy, R&D inspection and certification company, and included steel producer Feralpi Siderurgica, Tenova as a Technology Provider, I.BLU, an Iren Group company as SRA producer, and Strane Innovation, a French consulting company providing business/strategy analysis.
Preliminary investigations during OnlyPlastic identified injection as the most efficient way to use SRA, leading the Tenova R&D team to develop a new family of wall-mounted lances specifically designed to promote iron oxide reduction and slag foaming processes with low-density and high-reactive materials. Our new injection technology demonstrated the sustainability of producing steel by means of alternative carbon carriers without affecting the slag foaming and the EAF process stability with a lower environmental impact in terms of CO2 emissions and reduction of landfilling wastes.
Tenova Injection System
The injection of SRA into modern EAFs represents a significant technological challenge due to its low density and high reactivity. The carbon contained in the injected solid material reacts with iron oxide and oxygen at the slag-steel interface to produce CO. This gas, in the form of bubbles, allows the development and control of a foamy slag inside the furnace with a direct impact on the energy efficiency of the process (the arc is covered, reducing heat losses in the ambient) and on the product yield (the iron oxide is reduced to iron). OnlyPlastic was also an opportunity for Tenova to develop new solutions, like the Tenova KT® Multi. Based on the need to inject multiple solids simultaneously, the Tenova KT® Multi aims at simplifying the chemical package installation in complex layouts, reducing the number of injection points and, consequently, the number of openings in the furnace. This new solution, which will be available in both single and twin versions, will allow new and advanced process control practices, facilitating the adoption of SRA into the present EAF.
Strane’s analysis of the SRA supply chain highlighted that the geographical distribution of municipal waste collection/sorting facilities on the Italian territory would allow the creation of a virtuous supply chain based on an industrial synergy between the steel industry and plastic recycling plants. At the European level, a similar pattern is already in practice in other regions, such as northern Spain and the French-German border indicating the possibility of exporting the OnlyPlastic model.
A Life Cycle Assessment (LCA) study performed by RINA-CSM highlights the environmental benefits of using SRA in steel production: reduction of Scope 1 CO2 emissions by up to 30% (climate change), reduction of landfilling of hard-to-recycle plastic materials (land use), no impact on the air quality (particulate matter, ozone depletion, acidification).
Want to know more?
Get in touch with our experts on the subject